為推動電動汽車關鍵共性技術發展,服務于成員單位技術研發需求,自成立以來,聯盟一直持續開展整車及關鍵零部件前沿、共性技術研究工作,形成了大批研究成果,推動了電動汽車產業技術創新和進步。2023聯盟共立項共性技術課題22項,為推動課題交流和成果共享,聯盟將持續發布在研課題研究進展和成果,最大化發揮課題研究價值。
高性能驅動電機及關鍵材料技術研究課題由哈爾濱理工大學謝穎教授承擔,課題面向新能源汽車電機對高功率密度和高效率的需求,通過多學科交叉理論和實驗方法,解決電機設計中的科學問題,包括電機拓撲結構的優化設計和優選方法,以及新材料在電機設計中的設計準則,并通過電-磁-流-熱-聲多場協同設計,給出水油復合冷卻或直接油冷設計方案,完成低振動噪聲電機設計。
隨著車用驅動電機不斷發展,對電機性能提出了更高要求,并且在電機設計過程中需綜合考慮電-磁-熱-聲等多場域性能表現。首先根據性能要求與尺寸限制,確定電機的基本參數。通過有限元軟件maxwell對電機進行建模及仿真計算,電機有限元二維模型如圖1所示,電機定子采用扁線繞組,轉子永磁體采用雙V結構。
為研究不同繞組層數時扁線繞組交流銅耗情況,通過有限元仿真對比了8層和10層繞組在最高轉速16000rpm下的交流損耗,損耗密度分布結果如圖2所示。在給定額定電流以及最高轉速下,8層繞組和10層繞組的交流銅耗分別為1.32kW和1.10kW,10層繞組相比于8層可以降低約20%的交流銅耗,因此最終選擇10層扁線繞組。
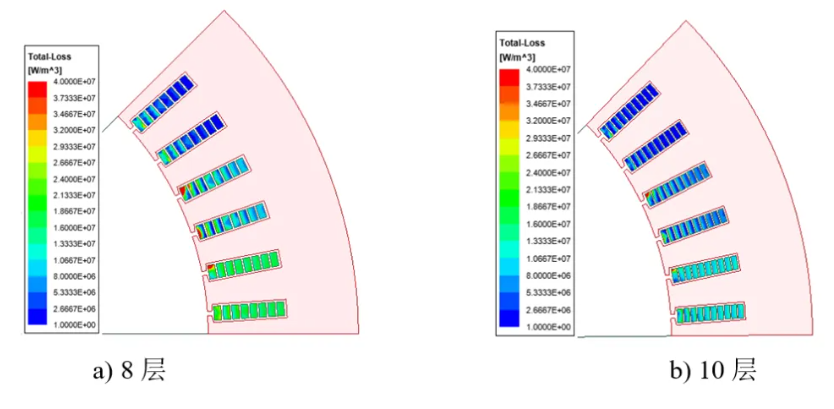
2. 電機電磁性能分析
為驗證電機性能是否滿足指標要求,采用有限元法對電機各方面電磁性能進行分析,首先針對電機空載工況進行仿真校核,電機空載反電勢及其諧波分布如圖3所示,可以看出空載反電勢呈正弦性分布,基波幅值為112V,諧波畸變率為4.67%。
永磁電機的齒槽轉矩對電機運行平穩性及振動噪聲等有著重要影響,故在永磁電機設計時需重點關注。仿真得出齒槽轉矩波形如圖4所示,齒槽轉矩峰-峰值為0.26N·m。
前文完成了電機空載工況下的仿真分析,接下來進一步對電機負載工況下運行狀態進行研究,主要分析電機的輸出轉矩情況。車用永磁同步電機通常追求較小的轉矩波動以保證電機運行的平穩性,狀態轉矩波動可表示為:
式中:Tripple為轉矩波動;Tmax為最大轉矩值;Tmin為最小轉矩值;Tavg為平均轉矩值。以有限元法得出電機額定及峰值工況下轉矩如圖5所示。
根據圖5可以得出電機額定和峰值工況下平均轉矩分別為105.4N·m和298.8N·m。滿足電機設計指標中的轉矩要求。此外,根據公式計算得出電機額定工況和峰值工況下的轉矩波動分別為4.6%以及5.9%。
通過有限元方法繪制出電機的效率MAP特性如圖7所示,可以看出電機最高效率為97.12%,高于電機設計要求。同時可以看到電機高效區域面積較大,計算得出電機效率大于80%的區域占總效率MAP圖面積的90%以上,最大效率區域集中在額定工況附近,證明了電機滿足技術指標要求。
對于車用永磁同步電機來說,在設計時除了要考慮電磁性能之外,還需要關注電機的轉子機械強度,電機最高設計轉速為16000rpm,并且內置式雙V型轉子結構中間磁橋部分和外部磁橋部分設計的相對較窄,在電機高速運行時受離心力的影響,有可能導致轉子結構損壞,影響電機的正常運行,為此有必要對轉子結構進行機械強度校核。通過仿真計算得到電機最高轉速及1.1倍最高轉速下轉子應力及形變如圖7所示。
可以看出此時電機轉子所受應力大于轉子硅鋼片的屈服強度,因此需要對其進行優化設計,優化后轉子結構如圖8所示
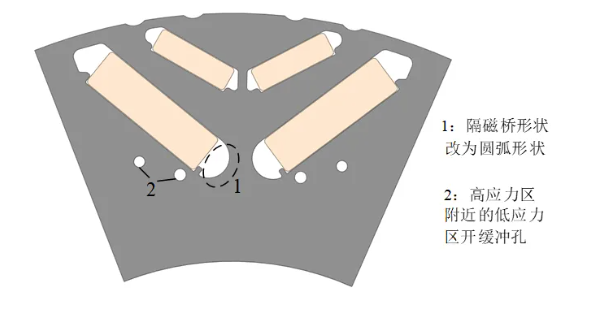
圖8 優化后轉子結構
轉子結構優化后的應力仿真分析結果如圖9所示,可以看出優化后的轉子結構在16000rpm時所受的最大等效應力為335.37Mpa,相比于優化前降低了104Mpa,優化后結構在1.1倍最高轉速下最大應力為405Mpa,仍未超出轉子硅鋼片屈服強度,可以看出,優化后的轉子結構在考慮安全裕量的情況下依然滿足安全可靠運行要求。
圖10給出所設計電機的三維模型及冷卻通道流體域模型。從圖中可以看出本研究中所設計的冷卻結構主要包括兩部分,一部分是定子背部環形冷卻通道,用于冷卻定子鐵心。另一部分繞組端部淋油冷卻。
本研究中所設計冷卻結構包含定子背部油路以及端部淋油結構兩部分,由于兩部分冷卻結構為串聯式設計,兩部分流量總和即為入口流量,所以確定其中一部分流量即確定了整體的流量分配情況。首先針對定子背部油路進行詳細的流場仿真分析。
雖然匝數對于定子背部油路流量影響很小,但不同匝數下定子背部油路的散熱效果會受到流速、流阻、等流體參數影響,因此建立了只包含定子鐵心與冷卻結構的溫度場計算模型如圖11所示,仿真過程中值考慮定子鐵耗,通過CFD方法計算得出不同油路匝數下定子溫度并研究不同油路匝數下的散熱效果,溫度分布如圖12所示。
可以看出,當定子背部厚度同為2mm時,隨著油路匝數的增多定子溫度逐漸降低,因此最終確定定子背部油路厚度為2mm,匝數為8匝。接下來將著重分析冷卻結構的端部淋油特性。
針對不同噴油孔直徑和數量下的流場特性及噴油效果進行了研究,選擇噴油孔數量為9個或11個,如圖13所示。此外,選取噴油孔直徑為1.5mm,2mm,2.5mm,3mm四種尺寸。所以共得出8種噴油孔設計方案如表2所示,首先針對8種方案進行噴油環壓力分析,結果如圖14所示。
表2 噴油孔設計方案
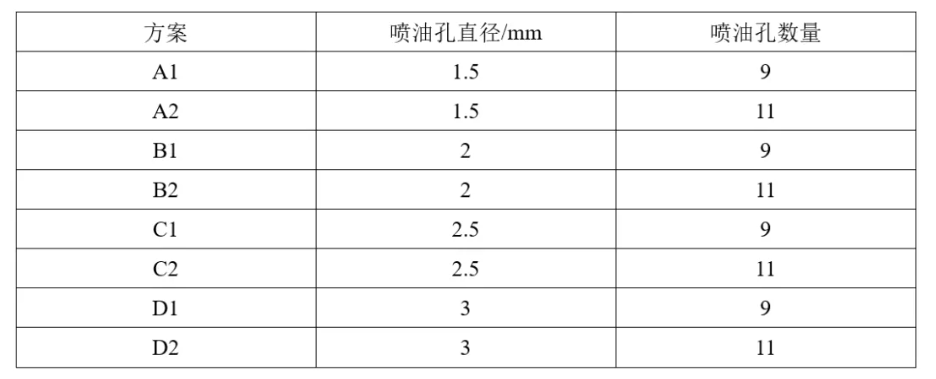
從圖14可以看出,噴油孔的孔徑越小,壓力越大,噴油環及噴油孔的壓力分布越均勻。與此同時,在孔徑相同的情況下,布置9個孔時噴油環的壓力略高于布置11個孔時。這說明了9個孔的平均噴淋流速要大于11個孔。此外,為了量化噴油孔直徑和數量兩個因素對噴油效果的影響,表3給出了具體的流量分布結果。
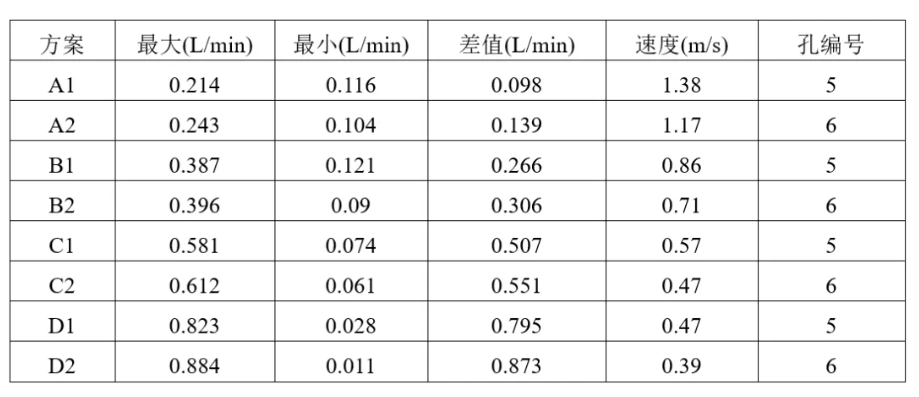
由表3可以看出,從方案A1到方案D2,噴油孔中的最大流量呈現逐漸增大趨勢,最小流量呈現逐漸減小趨勢,因此兩者之間的差值也逐漸增大。同時,噴油孔的平均噴射速度逐漸降低。
為了研究孔徑和孔數對冷卻結構噴油效果的影響,設計了可更換噴油孔的電機殼體,如圖15所示。該電機殼體采用3D打印方法構建,可進行不同孔數量及排布方式下的油路實驗驗證。
首先針對8個方案依次進行實驗分析,觀測噴油效果并對噴油孔的流量進行測量,在實驗中觀測到的各方案下的噴油性能表現如圖16所示??梢钥闯?,從方案A到方案D,噴油效果明顯減弱,這與仿真結果是一致的。此外,由于在方案C和方案D中,從孔中緩慢溢出的油無法被量杯收集,因此最小流量記錄為零,這將導致誤差增加。
另外,圖17給出了仿真和實驗得到的最大流量差對比,并在圖17中標注了仿真結果相較于實驗結果的誤差??梢钥闯?,仿真和實驗得到的最大流量差變化情況是一致的,均隨著孔徑的增大而呈現出明顯的增大趨勢。方案A和B的誤差小于5%。
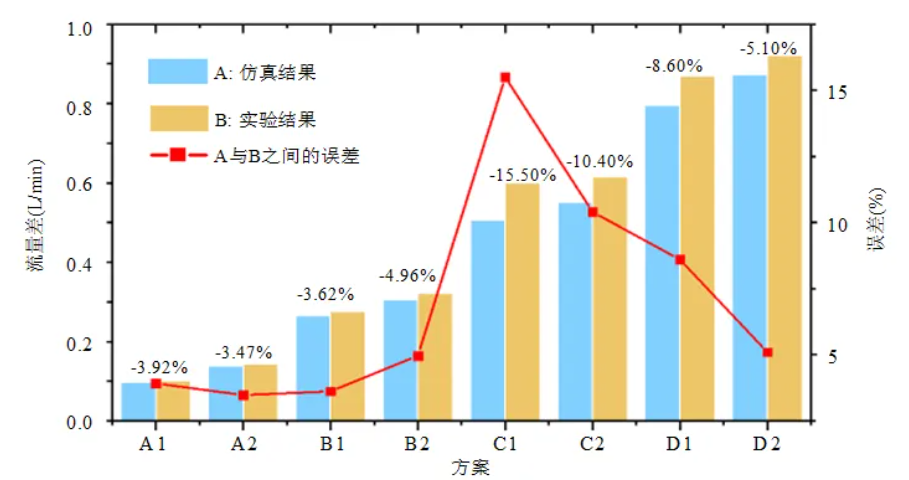
圖17 仿真和實驗得到的最大流量差
為了研究噴油性能對電機溫度的影響,接下來通過粒子法、流固耦合溫度場分析方法對不同噴油方案下的繞組端部油膜覆蓋率和電機溫度場情況進行詳細分析。
在傳統的溫度場計算方法中,繞組端部通常被等效為實心圓環從而降低建模難度,減少網格數量以及加快計算速度。但對于發卡式繞組淋油冷卻永磁同步電機來說,等效的繞組端部不能準確地表征冷卻油在繞組端部的縫隙及層間的流動狀態及換熱過程,會極大地降低求解精度,因此本文建立了接近真實情況的繞組端部模型,以準確獲得冷卻油在繞組端部的分布情況并提高溫度場計算精度。圖18中給出了本文建立的模型以及與傳統等效模型的對比。
圖18 傳統等效繞組模型以及本文建立的準確繞組模型對比
基于建立的精確繞組模型,應用運動粒子法仿真軟件對繞組端部的油膜覆蓋率進行求解,求得方案A1,A2,D1下的插線端繞組端部油膜覆蓋情況如圖19所示。
可以看出,由于方案A1和方案A2噴油效果較為均勻,方案A1和A2的繞組端部油膜覆蓋率明顯高于方案D1。三種方案繞組插線端的油膜覆蓋率分別為30.48%、27.88%和13.24%。
選取方案A1,A2,D1這三種方案進行溫度場計算分析,電機溫度場計算結果中溫度分布如圖20所示。電機各部件最高溫度在表4中給出。從圖20可以看出,繞組溫度分布與油膜覆蓋范圍一致,可以得出方案A1溫度最低,高溫區域的面積最小且溫度最低,溫度分布也更加均勻。
表4 電機各部件最高溫度(℃)
本文所設計電機技術指標要求峰值工況下運行15s,因此采用冷卻方案A1對電機峰值工況進行了瞬態溫度場計算,結果如圖21所示。
可以看出由于峰值工況繞組損耗的急劇增大,電機繞組在15s時間內升高到157.5℃。而轉子及永磁體由于損耗不大,溫度不超過120℃??傮w來說,電機各部件溫升在合理范圍內,不易發生絕緣劣化以及退磁等故障,進一步證明了本文電機設計的合理性。