為推動電動汽車關鍵共性技術發展,服務于成員單位技術研發需求,自成立以來,聯盟一直持續開展整車及關鍵零部件前沿、共性技術研究工作,形成了大批研究成果,推動了電動汽車產業技術創新和進步。2023聯盟共立項共性技術課題22項,為推動課題交流和成果共享,聯盟將持續發布在研課題研究進展和成果,最大化發揮課題研究價值。
動力電池低溫快速加熱技術課題由北京新能源汽車股份有限公司承擔,課題主要針對電動汽車鋰離子動力電池在低溫下工作時,電池內阻明顯升高、功率和能量急劇下降,導致低溫環境下整車充電時間增長、動力性能受限、續航衰減明顯等問題,提出低溫快速加熱技術方案,突破三維電熱耦合仿真技術、多因素交叉尋優驗證技術、脈沖大電流激勵技術、車樁互聯閉環控制技術等9項關鍵技術,優化低溫充電、低溫行車、駐車保溫3大場景用車體驗,形成覆蓋整包級、充電樁級、整車級的序列化低溫速熱技術規范,搭建車樁互聯平臺,推動示范運營及產業化。
本項目通過基于AMESIM建立系統一維仿真模型,基于STAR-CCM+建立CFD仿真模型,并通過COSIM方式耦合仿真模型,在一維仿真模型中建立電模型計算電芯電壓、電流、及發熱功率,并將發熱功率反饋給CFD仿真模型,CFD仿真模型將電芯最高溫度、最低溫度反饋給電模型,并在一維仿真模型中設置熱管理控制策略,根據電芯最高及最低溫度執行,具體仿真架構如下圖所示:
電熱耦合仿真模型優勢在于一維電芯模型通過不同SOC、不同溫度HPPC測試數據進行二維等效電路模型參數辨識,可得到電芯歐姆內阻、極化內阻、擴散內阻參數,因此電芯發熱功率計算準確,同時通過三維仿真模型的最高及最低溫度的實時反饋,實現電熱耦合模型的動態仿真,可極大提高系統溫度仿真精度。
圖2 電池系統最高及最低溫度對比
如圖2所示,電池系統最高及最低溫度仿真精度控制在2℃以內,如圖3所示電芯內阻仿真精度控制在3%以內。
構建一種從電熱耦合仿真到多因素交叉邊界驗證的標準化尋優方法,在電芯析鋰及壽命邊界限制下,尋找實時優化的電流幅頻控制策略,如圖4所示為脈沖加熱充電電流map及放電電流map。在高頻脈沖模式下,電芯經過耐久測試,驗證在脈沖加熱模式下電芯壽命影響。電池經500次加熱循環后容量保持率仍≥99%,且電芯進行拆解,電芯無析鋰現象,表明在高頻脈沖加熱模式下,電芯全壽命周期內基本無壽命衰減現象。
圖4 電芯充電及放電電流邊界
在確定電池系統脈沖加熱電流map基礎上進行整車低溫環境脈沖加熱測試,對比測試結果如圖5所示。在-30~0攝氏度范圍內,電池系統樁端脈沖加熱速率均在5℃以上,較WTC加熱0.8~1℃/min的加熱速率提升4倍以上。同時進行低溫快充測試,相同工況下樁端脈沖加熱方式較常規WTC加熱方式快充時間減少20%~49%,可見通過脈沖加熱及快充的方式可極大縮短低溫環境充電時間,降低用戶低溫環境充電等待時間長焦慮。
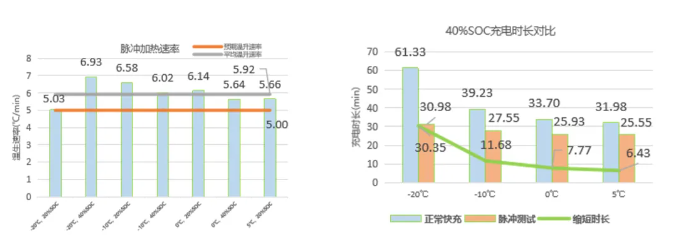
圖6 脈沖加熱速率及低溫快充時間
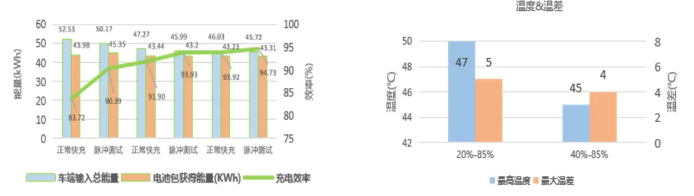
4. 脈沖加熱超充樁建設
在樁端激勵源方面,選用雙向高頻DC/DC模塊作為脈沖電流激勵源,超級電容作為短時儲能單元,匹配高功率極狐超充終端,通過自研的脈沖加熱通訊協議,實現高頻脈沖電流的輸出/輸出。脈沖加熱流程圖如圖7所示。在車樁聯調方面,通過車樁通訊協議、整車功能定義、樁端充電協議的開發,實現車樁信號通信和速加熱功能實現。通過車樁雙工況自識別控制策略及基于前饋補償的SOC在線估算算法,優化脈沖速加熱模式下SOC和充電剩余時間估算。
整車脈沖加熱測試數據如下圖所示,脈沖加熱完成后即進入快充過程,且在脈沖加熱過程中電池系統SOC基本無變化,且加熱過程中電池系統溫差控制在3℃以內??梢姌抖嗣}沖加熱是解決低環境低溫充電時間慢的有效方案。
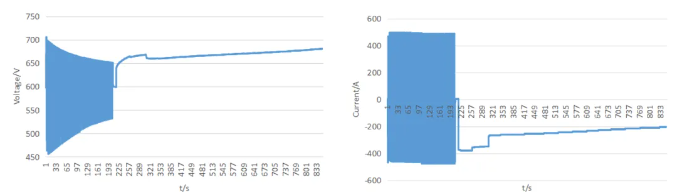
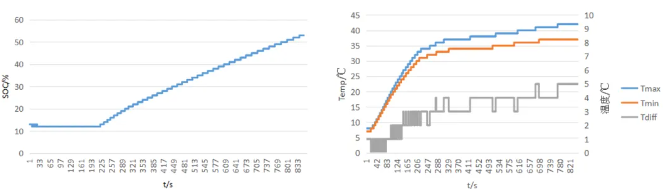
目前脈沖加熱超充示范站如下圖13所示。
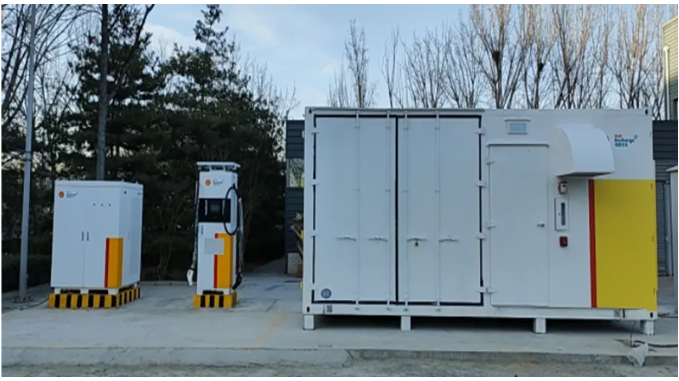
1.針對不同電芯類型的脈沖加熱進行測試及數據分析,積累脈沖加熱數據庫;
2.進行樁端脈沖加熱超充樁示范的應用推廣;